In the world of industrial operations and manufacturing, plant maintenance has always been a critical function. Ensuring the smooth functioning of machinery, minimizing downtime, and maximizing efficiency are essential to the success of any production facility.
However, the landscape of plant maintenance has evolved significantly in recent years, thanks to advancements in technology. From predictive analytics to the integration of robot assistants, technology is reshaping the way we approach plant maintenance and helping to usher in a new era of efficiency and productivity.
The Traditional Challenges of Plant Maintenance
Before delving into the transformative impact of technology, let's first understand the traditional challenges faced by plant maintenance professionals. Historically, maintenance practices have often been reactive rather than proactive. This means that maintenance teams would wait until equipment broke down or showed signs of wear and tear before taking action. This approach resulted in unplanned downtime, costly repairs, and a loss of productivity.
Additionally, plant maintenance traditionally relied on manual inspections and routine checks, which can be labor-intensive and prone to human error. Maintenance teams had to rely on their experience and expertise to identify potential issues, which sometimes led to oversight or delayed responses to critical problems.
The Rise of Predictive Analytics
One of the most significant advancements in plant maintenance technology is the adoption of predictive analytics. Predictive maintenance leverages data and machine learning algorithms to predict when equipment is likely to fail. By continuously monitoring the condition of machinery and analyzing historical data, maintenance teams can identify patterns and anomalies that indicate potential issues.
Predictive analytics allow maintenance professionals to take a proactive approach by addressing problems before they lead to equipment failure. This not only reduces unplanned downtime but also extends the lifespan of machinery and lowers maintenance costs. It's a win-win situation for both plant operators and maintenance teams.
Here are some key elements of predictive analytics in plant maintenance:
Data Collection: Sensors and IoT (Internet of Things) devices are installed on machinery to collect real-time data on factors like temperature, vibration, and fluid levels. This data is continuously transmitted to a central system for analysis.
Machine-Learning Algorithms: Machine-learning algorithms process the data to identify patterns and anomalies. These algorithms can predict when equipment is likely to fail based on historical data and current conditions.
Alerts and Notifications: When the algorithms detect potential issues, maintenance teams receive alerts and notifications. These alerts can be prioritized based on the severity of the issue, allowing teams to focus their efforts where they are most needed.
Prescriptive Actions: Predictive maintenance systems can also provide recommendations for corrective actions. This might include scheduling maintenance tasks or ordering replacement parts before a failure occurs.
The adoption of predictive analytics has transformed plant maintenance from a reactive to a proactive discipline. It empowers maintenance teams to make data-driven decisions and optimize the use of resources, ultimately leading to improved plant efficiency.
Robot Assistants in Plant Maintenance
While predictive analytics has been a game-changer, another exciting development in plant maintenance is the integration of robot assistants. Robots are being used to perform a variety of tasks in industrial settings, including inspection, maintenance, and even repairs. Here's how robot assistants are reshaping plant maintenance:
Routine Inspections: Robots equipped with cameras and sensors can autonomously inspect equipment and infrastructure. They can access hard-to-reach areas and capture high-resolution images and data. This information is invaluable for detecting early signs of wear and tear.
Predictive Maintenance Support: Robots can work in tandem with predictive maintenance systems. When an alert is generated, a robot can be dispatched to the affected area to perform a more detailed inspection and gather additional data. This helps maintenance teams make more informed decisions about the necessary repairs or replacements.
Maintenance and Repairs: Some robots are designed to perform routine maintenance tasks or even minor repairs. For example, a robot equipped with a 3-D printer can fabricate replacement parts on-site, reducing downtime.
Safety: Robot assistants can be deployed in hazardous environments where it might be unsafe for humans to work. This not only enhances safety but also allows for more frequent and thorough inspections in these areas.
Training and Skill Transfer: Robots can be used to train new maintenance technicians. They can simulate various maintenance scenarios and provide hands-on training without the risk of damage to equipment or injury to personnel.
Challenges and Considerations
While the integration of technology in plant maintenance offers numerous benefits, there are also challenges and considerations to keep in mind:
Cost: Implementing predictive analytics and robot assistants requires a significant initial investment in technology and training. However, the long-term cost savings often justify this expense.
Data Security: Protecting sensitive maintenance data from cyber threats is crucial. Robust cybersecurity measures are essential to safeguard the integrity of predictive maintenance systems.
Integration: Ensuring that predictive maintenance systems and robot assistants seamlessly integrate with existing plant infrastructure and processes can be complex but is necessary for their effectiveness.
Human Expertise: While technology can automate many tasks, human expertise is still essential in interpreting data, making decisions, and handling complex maintenance scenarios.
Regulatory Compliance: Industries may be subject to regulatory requirements that dictate maintenance practices. Ensuring that technology implementations meet these standards is vital.
The Future of Plant Maintenance
As technology continues to advance, the future of plant maintenance looks promising. Predictive analytics and robot assistants are just the beginning. Artificial intelligence, augmented reality, and remote monitoring are also becoming integral parts of maintenance strategies.
Augmented reality, for example, can provide on-site technicians with real-time information and guidance through smart glasses or mobile devices, making complex repairs more accessible. Remote monitoring allows experts to analyze data from multiple facilities, offering insights and recommendations from afar.
The insights and data these technologies provide play a vital role in the modern functioning of most plants and facilities. Being able to embrace and integrate these technologies can make all the difference in your plant going from good to great.
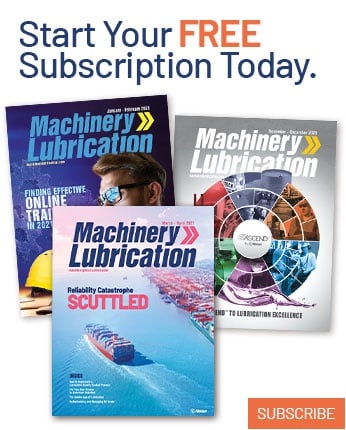